Infrastructure
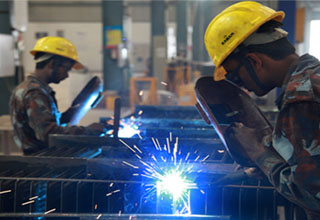
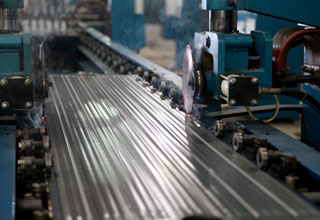
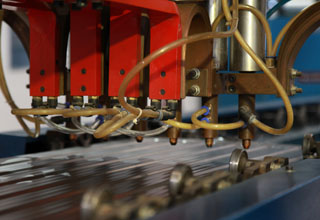
We have 4 Overhead EOT cranes(7.5 MT ,3 MT , 2 MT & 5 MT) for proper handling of the Job . The Unit has state of the art facilities for the manufacturing and proper testing of Radiators owing to our commitment towards quality and client satisfaction .
The Automatic Production Line :
The Production line is 146ft in length with all the settings provided to form panels of width 520mm and length varying from 1000mm to 4000 mm . Our radiators conform to the prevalent DIN 42559/ IEEEMA 9:1990 standards and customer's specifications.
The Radiators are suitable for usage in Oil Natural Air Natural (ONAN) and Oil Natural Air Forced (ONAF) conditions
The panels are formed without any human intervention in a dust free environment by the Fully Automatic PLC Controlled Production Line .
Jigs And Fixtures :
We have specially designed hydraulically and pneumatically controlled Jigs and Fixtures( for flange welding , Pipe Cutting etc) so as to achieve the required precision.
We also possess automatic pipe cutting machines for 80 NB / 100 NB pipes to cut the pipes accurately for different kinds of Radiators.
Shot Blasting :
We realize that shot blasting is a very important process to achieve quality surface for further coatings of Primer , Intermediate and Final coat . We possess an advanced blast room facility incorporating:
• Cyclone dust collectors so as to separate dust from fine abrasive particles
• Mechanical Recovery System consisting of Bucket Elevator , Abrasive Cleaner and Screw Conveyer System
• "U" shaped Partial Reclaim System to meet safety and environmental concerns of our customers.
Paint Shop :
We possess a state of the art, completely dust free, paint shop for achieving a proper and even coat over the panel surface at all points so that our customer gets the desired DFT as per their specifications .
The Paint shop also achieves proper filtration and re-circulation of excess coated material so as to meet impeccable quality.